Supermarket Shelving – Leading Supplier Italy
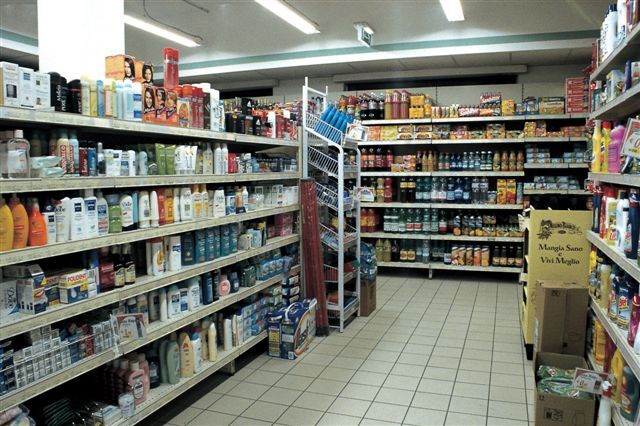
Introduction to Supermarket Shelving
Why Shelving Is Crucial in Supermarkets
Shelving forms the backbone of every modern supermarket, transforming simple commercial spaces into organized and functional environments. Its importance goes well beyond just product display: shelving directly influences customer flow, optimizes operational processes, and significantly contributes to sales results. Well-designed shelving facilitates consumer navigation, reduces restocking times, and ensures high safety standards.
The effectiveness of a shelving system is measured by its ability to maximize the use of available space while maintaining accessibility and order. This balance becomes crucial considering that Europe holds a substantial 28% share of the global shelving market, with growth driven by strong economies and demand for innovative solutions.
Choosing the right shelving affects every aspect of the shopping experience. As industry experts highlight, manufacturers develop versatile, modular shelving systems that allow for easy customization and reconfiguration—meeting the dynamic needs of retail spaces. This adaptability is a fundamental competitive advantage for retailers who must quickly respond to market changes, especially since food retail sales in Italy increased by 18.1% from 2019 to 2024.
Current Trends and Innovations in Shelving Design
The supermarket shelving sector is undergoing an accelerated transformation, driven by technological innovation and new consumer needs. The global retail shelving market reached USD 4.03 billion in 2025, with Europe identified as a key region for steady growth.
Key innovations involve integrating smart technologies for inventory management and the adoption of eco-sustainable materials. Modern shelving systems incorporate weight sensors, RFID readers, and connected analytics platforms to enable continuous product monitoring, automated low-stock alerts, and integration with POS systems. A concrete example of this evolution is Walmart’s large-scale implementation of electronic shelf pricing technology in 500 additional stores in May 2023, which enabled greater pricing flexibility, reduced manual labor, and improved customer interaction.
The global retail shelving systems market is projected to grow at a CAGR of 9.2% from 2025 to 2032, rising from USD 2.64 billion in 2025 to USD 4.89 billion by 2032. This trend reflects the increased adoption of modular and customizable solutions, adaptable to spaces of various sizes and configurations.
As industry analysts point out, integrating smart technology into shelving systems offers significant growth potential, allowing for real-time inventory monitoring, automated restocking, and data-driven decision-making. Another emerging trend is the increasing focus on aesthetics and customer experience, with retailers investing in shelving that not only organizes products but also creates engaging, immersive environments.
Types of Supermarket Shelving
Metal Shelving: Versatility and Strength
Metal shelving is the predominant choice for supermarkets due to its exceptional robustness and superior load capacity. Made primarily from high-strength steel, these structures guarantee long-term durability and operational safety even in high-traffic environments.
The versatility of metal shelving is evident in the ability to configure shelves, accessories, and components according to the store’s specific needs. Systems like those developed by CAEM Group—a sector leader based in Subbiano—offer solutions such as the M25 system with a central optimized back panel and 25 mm slotting system for precise shelf placement, or the sturdy S50 system compatible with 50 mm standard fixtures and load capacity up to 1000 kg per level.
Ease of assembly and modification is a significant competitive advantage. Modern metal shelving allows for quick reconfiguration without special tools, supporting dynamic adaptation to commercial needs. Surface treatments such as galvanization, powder coating, or plastic finishes ensure corrosion resistance and color customization to match brand identity.
Modular Shelving and Its Flexibility
Gondola shelving, recognized for its versatility and modularity, remains the most widely adopted system in retail environments for its ability to flexibly adapt to evolving product assortments and variable store formats.
Modular systems represent the natural evolution of traditional shelving, offering unlimited composability and scalability according to available dimensions. This type enables custom configurations by assembling standardized elements, ensuring economies of scale in production and flexibility in implementation.
Modularity significantly simplifies the integration of specialized accessories such as dividers, displays, supports for specific products, and lighting systems. CAEM’s TN9 system, for example, stands out for its stability, adaptability, and wide range of color options and plastic finishes, available in various heights to suit any store configuration.
Quick assembly and easy customization are tangible advantages for supermarkets of all sizes. The ability to easily expand or reduce shelving allows for effective response to seasonal changes, special promotions, or layout reorganizations without significant investment in new structures.
Custom Shelving: Personalization for Unique Spaces
Custom shelving is the ideal solution for supermarkets with particular architectural features or specific needs that cannot be met by standard systems. This approach allows every centimeter to be utilized, even in irregular or complex environments, maximizing display area and optimizing customer flow.
Customization involves all aspects of the system: dimensions, materials, finishes, accessories, and configurations. Specialized suppliers like CAEM offer advanced customization capabilities, with shelving available in at least 15 standard colors, custom dimensions, and just-in-time painting processes to rapidly respond to personalized orders.
The tailored approach allows design elements to be integrated that reflect brand identity and enhance the shopping experience. Custom design can incorporate innovative solutions such as integrated LED lighting, surfaces with specific treatments for different product types, or optimized configurations to facilitate restocking operations.
Relying on experienced manufacturers ensures functional, safe results consistent with corporate image. Direct collaboration during the design phase anticipates issues and optimizes solutions for the store’s specific operational conditions.
Eco-Sustainable Shelving Systems
The growing preference for shelving made from recycled or responsibly sourced materials reflects the increasing importance of sustainability in retail purchasing decisions. This trend aligns with corporate social responsibility initiatives and consumer demand for greener stores.
Eco-sustainable systems maintain high standards of quality, safety, and durability without compromising functionality. Innovative manufacturers are developing fully modular shelving that allows for easy reconfiguration, ergonomic improvements, and adaptability to evolving retail needs, avoiding the limitations of traditional wooden units.
Attention to ecology extends beyond materials, involving low-impact production processes, non-toxic paints and treatments, optimized transportation, and sustainable logistics. CAEM demonstrates this commitment by reducing its environmental footprint with solar panels, adopting energy-efficient technologies, preferring rail imports to reduce emissions, and participating in annual tree-planting programs.
Investment in sustainable systems adds value to store image and helps retain customers increasingly sensitive to environmental issues. These systems also support circular economy strategies, enabling reuse, reconfiguration, and recycling at end of life.
Challenges and Solutions in Implementing New Shelving Systems
Common Obstacles and How to Overcome Them
Implementing new shelving systems presents significant challenges requiring careful planning and specialized expertise. Industry experts identify implementation costs as the main barrier, especially when integrating advanced digital technologies and high-quality materials requiring significant initial investment both for hardware and staff training.
Technical complexity is another critical challenge. Adoption of technologies such as IoT, sensors, and RFID requires robust IT infrastructure and ongoing support to ensure data accuracy and system reliability. This complexity can intimidate supermarket managers less experienced with technology.
The rapid evolution of consumer preferences adds further pressure. Retail design teams must remain agile as consumers’ expectations for store aesthetics and convenience change rapidly, requiring frequent updates to layouts and shelving features to remain competitive.
To overcome these obstacles, supermarkets should adopt a gradual approach, implementing improvements in phases rather than immediate complete transformations. Partnering with experienced suppliers who offer training, technical support, and scalable solutions greatly eases the transition and reduces operational risk.
Practical Guide for Supplier Evaluation
Selecting the ideal supplier requires a structured process considering several critical factors. Start by assessing established experience in the supermarket shelving sector, analyzing project portfolios, client references, and market presence. Request concrete examples of installations similar to your store format and size.
Verify the range of services offered beyond product supply. The best suppliers should include design consultancy, technical site surveys, 3D design, prototyping, professional installation, and maintenance services. Certifications such as ISO 9001:2015 ensure internationally recognized quality standards.
Analyze customization capabilities and response times for specific orders. Suppliers like CAEM, with just-in-time painting processes and over 15 standard colors available, demonstrate operational flexibility essential for time-sensitive projects. Also assess geographic presence and the availability of local technical support for rapid interventions.
Request detailed quotes including all associated costs: products, transportation, professional installation, staff training, and after-sales support. Compare not only prices but also the overall value of the offer, considering durability, warranties, included services, and long-term operating costs.
Budgeting and Implementation Timeline Considerations
Accurate financial planning is crucial for successful implementation. Besides shelving costs, consider ancillary expenses such as transportation, professional installation, any store structural modifications, staff training, and possible operational disruptions during installation.
Implementation times vary significantly depending on project complexity. Standard projects with modular shelving may take 2–4 weeks from order confirmation to delivery, while fully customized solutions may require 6–12 weeks. Always plan safety margins for unforeseen events or delays.
To minimize commercial impact, consider phased implementation by store section, night installations, or during lower-traffic periods. Some suppliers offer rapid installation services that allow entire sections to be completed overnight, reducing operational disruptions.
Evaluate financing options such as operating leases or installment plans that allow investment to be spread over time, preserving company liquidity. Many suppliers offer flexible financial solutions to facilitate access to advanced technologies even for medium-sized supermarkets.
Sustainability Certifications and Regulatory Compliance
Mandatory European Standards for 2024–2025
Compliance with European regulations has become fundamental for shelving systems marketed in Italy and the rest of Europe. The Ecodesign for Sustainable Products Regulation (ESPR) takes effect in July 2024, with the first work plan published in April 2025, setting minimum requirements for product durability, recyclability, and energy performance.
The regulation imposes restrictions on hazardous substances and requires improvements in product circularity and repairability. Commercial shelving may be classified as furniture or commercial equipment, making compliance mandatory for all products placed on the EU market, directly affecting manufacturers, importers, and distributors.
At the same time, the General Product Safety Regulation (GPSR) has been in force since December 2024, replacing the previous directive. All non-food consumer products must be safe and subject to internal risk assessments, requiring technical documentation to support safety claims for new, used, repaired, and refurbished products.
The Product Environmental Footprint (PEF) Framework
The PEF is becoming the benchmark method for environmental assessment under the European Green Deal and ESPR by 2025. This framework requires comprehensive life cycle assessments (LCA) covering carbon impacts, water use, resource consumption, and total environmental impacts.
Alignment with Product Category Rules (PCRs) ensures sector consistency in assessments. While not yet strictly mandatory everywhere, PEF is increasingly required for product declarations and eco-labeling, especially for companies supplying public contracts or environmentally conscious retailers.
Adoption is growing rapidly, especially among companies serving public contracts or eco-conscious retailers. Full adoption is expected as PEF is integrated into EU regulations, though SMEs may face challenges due to the complexity and data requirements for compliance.
Voluntary Certifications of Value
ISO 14001 certification for environmental management systems remains widely recognized internationally and is a credible baseline for environmental reliability. It requires implementing a formal environmental management system with a commitment to continuous improvement, regulatory compliance, management of significant environmental aspects, and transparent reporting.
Adoption is high among leading furniture and retail equipment manufacturers, providing a solid foundation for partnerships with suppliers and supply chains. ESG and corporate sustainability standards such as GRI, SASB, and ISO 26000 are often used by large retailers and manufacturers to demonstrate broader commitments to sustainability and governance, increasingly required by investors and major retailers.
ISO 26000 focuses on social responsibility, while GRI and SASB address environmental and social impact reporting. While voluntary, these frameworks are growing in importance, especially among public companies facing increased stakeholder pressure for sustainability transparency.
Benefits of Collaborating with an Italian Supplier
Quality and Certification of "Made in Italy" Shelving
Shelving produced in Italy benefits from a well-established reputation for exceptional quality, rooted in a tradition of craftsmanship passed down through generations. This heritage is widely recognized as essential for maintaining product excellence and brand storytelling, with luxury brands actively acquiring Italian suppliers to secure these specialized skills.
CAEM UK’s ISO 9001:2015 certification demonstrates a commitment to internationally recognized quality management standards. This certification highlights a focus on consistently delivering high-quality products and services, ensuring continuous improvement in operations.
Italian manufacturers stand out for integrating advanced materials, modularity, and experiential design, meeting current demands for customization, flexibility, and visually impactful retail spaces. The ongoing commitment to improvement reflects a focus on process optimization and customer satisfaction, designed to consistently meet customer requirements, build trust, and support long-term relationships.
Certifications ensure compliance with European and international regulations—a fundamental requirement for supermarkets aiming for operational excellence. The combination of craftsmanship and technological innovation results in durable, high-performing solutions that justify long-term investments.
Benefits of Local Support and On-Demand Design
Collaborating with an Italian supplier offers significant operational advantages due to geographic and cultural proximity. Fast response times facilitate all project phases, from initial design to final delivery and installation. The presence of technical and logistics teams in the region ensures comprehensive, personalized service.
Direct support enables effective communication, solution customization, and flexible management of changes or unforeseen events during implementation. Proximity also allows for on-site visits, detailed surveys, and specialized technical advice that optimize the final result.
On-demand design is a hallmark of Italian suppliers, enabling the development of shelving perfectly integrated with the store’s specific needs and commercial strategy. This customization capability results in unique solutions that maximize operational efficiency and visual impact.
Direct collaboration throughout the process ensures results aligned with expectations and supports the development of long-term partnerships. The added value of "Made in Italy" is reflected not only in the final product’s quality but also in the overall collaboration experience.
Case Study: Documented Successes in the European Market
Italian supplier Movisi has demonstrated significant success by partnering with major European retailers to promote its modular BUILD shelving and divider system. In 2025, BUILD received the PETA Vegan Homeware Award as the best vegan shelving system, highlighting its success in sustainable retail collaborations in Germany and other European markets.
The system is fully recyclable and free of animal-based materials, meeting the needs of environmentally conscious retailers and consumers. Movisi was also selected as a finalist for the German Sustainability Award, further underlining its market impact and strong partnerships in the European retail sector.
Export data show that Italian shelving manufacturers have significantly expanded supplies to major European retailers. Export records through April 2025 document 224 Italian producers regularly supplying shelving products to prominent European buyers, demonstrating strong, ongoing collaborations with major supermarket chains and home goods stores.
These successes reflect Italian suppliers’ ability to combine innovation, sustainability, and specialized technical support. Documented partnerships through export data and supplier directories demonstrate the reliability and competitiveness of the Italian industry in the European retail shelving market.
How to Choose the Ideal Shelving Supplier
Criteria for Selecting a Reliable Partner
Established experience in supermarket shelving is the first indicator of reliability, along with a reputation built through completed projects and client feedback. The range of products offered should be broad enough to cover diverse needs while allowing for advanced customization.
Suppliers like CAEM, with a history dating back to 1958 and a global presence through production sites in Italy, the UK, Australia, and India, demonstrate the ability to effectively serve diverse markets while maintaining consistent quality standards. Certifications are a key selection factor, with ISO 9001:2015 certification and adherence to current safety and regulatory standards ensuring professionalism and compliance.
The ability to offer integrated services from consultancy to design, prototyping, installation, and shopfitting services is a significant added value. Guaranteed delivery times and ongoing assistance throughout the project phases complete the profile of the ideal partner.
The availability of both standard and customized solutions, with rapid response times for custom orders, demonstrates operational flexibility and customer service orientation. Also evaluate the presence of verifiable references and transparency in sharing case studies and results achieved with other clients.
Importance of After-Sales Support and Maintenance
Efficient after-sales service is essential for ensuring operational continuity and maximizing return on investment. Prompt technical support allows for rapid resolution of issues, implementation of changes, management of expansions, or necessary replacements without significant business interruptions.
Regular shelving maintenance extends system lifespan and ensures maintenance of required safety standards. Preventive and predictive maintenance programs help identify potential problems before they become critical, reducing operating costs and safety risks.
The availability of original spare parts and the presence of specialized personnel in the area are tangible indicators of after-sales service quality. Suppliers with established support networks guarantee rapid interventions and reliable solutions for any operational needs.
Support for inventory management and refurbishment services offer opportunities to keep shelving systems up-to-date and continually optimize store performance. These services add value that supports retail business growth and evolution.
The Importance of Customer Reviews and Testimonials
Customer opinions and testimonials provide valuable, objective information for evaluating a supplier’s reliability and actual quality. These sources offer concrete insights into the collaboration experience, service level, and general satisfaction that go beyond commercial communications.
Positive testimonials strengthen the supplier’s reputation and provide tangible evidence of the ability to meet expectations and deliver promised results. Analyzing feedback from other supermarkets helps identify distinctive strengths and excellence areas of the commercial partner.
Detailed reviews can reveal specifics such as material quality, delivery precision, staff technical competence, and after-sales effectiveness. This information supports more informed decisions and reduces risks associated with supplier selection.
Transparency in sharing references and case studies demonstrates confidence in the quality of service offered and a willingness to be evaluated based on results achieved. Suppliers who actively promote testimonials and feedback demonstrate a customer satisfaction orientation and commitment to continuous improvement.
The Future of Supermarket Shelving in Italy
Integration of Smart Technologies into Shelving
Retailers are integrating smart shelves with IoT sensors and AI algorithms to enable real-time inventory monitoring, predictive analysis, and dynamic stock replenishment. This automation helps reduce stockouts, optimize orders, and drive personalized in-store promotions—directly addressing both operational efficiency and evolving consumer expectations.
The global smart shelving market was valued at USD 4.16–4.4 billion in 2024 and is projected to reach USD 15.4–36.4 billion by 2030–2034, with a CAGR of 23–24% over the next decade. The surge in adoption is evident across various retail segments—not just grocery but also specialty stores and automated/self-checkout concepts—with Europe currently leading regional growth.
Smart shelving systems increasingly serve as the backbone for omnichannel retail, connecting physical store inventory with e-commerce platforms. This integration provides unified inventory visibility and enhanced fulfillment capabilities, essential for modern retail supply chains managing both online and offline channels.
CAEM is already introducing innovations such as the Ardente universal LED lighting system, which can be retrofitted onto any metal shelving to improve product visibility, increase sales, and enhance energy efficiency—demonstrating the evolution toward smart, integrated systems.
Potential Developments and Future Trends in Italy
There is expected to be increasing adoption of automated solutions and vertical storage systems to optimize use of available space. Shelving design will continue to evolve toward increasingly flexible and customizable configurations, responding to the specific needs of different retail formats and product types.
Growing focus on energy efficiency and operating cost reduction will drive the development of systems integrated with LED lighting, motion sensors, and intelligent energy management. These developments will support both sustainability and economic optimization goals.
Closer collaboration between manufacturers and supermarkets will lead to the development of fully integrated and customized systems for specific local needs. This trend will favor Italian suppliers able to offer end-to-end services from design to implementation and ongoing support.
The rising demand for modular, customizable smart shelving solutions scalable across various store formats—from supermarkets to convenience stores and pharmacies—will create opportunities for suppliers specializing in adaptable, technologically advanced systems.
Sustainability as a Strength for Shelving Suppliers
Integration of circular and recyclable materials is a major transformation identified by sustainability experts and analysts in the European retail fixture sector. Manufacturers and retailers are increasingly investing in fixtures made from recycled metals, wood, and plastics, as well as modular systems that can be reused or easily reconfigured.
Stricter sustainability reporting standards—such as the EU’s Corporate Sustainability Reporting Directive (CSRD)—are pushing retailers to transparently document the sustainability of their store infrastructure. This is driving growing demand for trackable, low-carbon, and certified-sustainable fixtures.
Digitalization and smart fixture systems using IoT sensors and data analytics to optimize energy use, enable predictive maintenance, and support real-time inventory management are growing. These innovations help reduce emissions and material use throughout the fixture life cycle.
A trend is emerging toward modular, reusable, and rental fixture models. Retailers are adopting shelving systems that can be easily reconfigured for new layouts or reused across different locations, supporting circularity and reducing waste from frequent store renovations—aligning with broader consumer preferences for second-hand and rental goods in retail experiences.